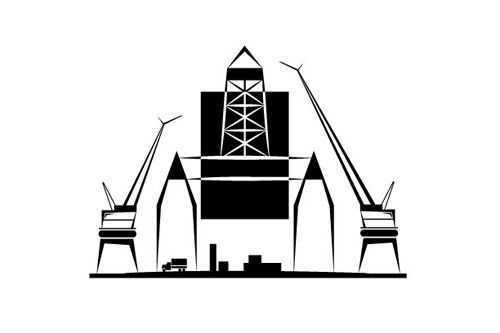
Drilling Equipment
Dynamic Brakes
1999
When the industry moved offshore into waters requiring subsea blowout preventers (BOP) and marine risers, it was no longer considered safe to use hydromatic brakes to control the huge weights involved. F. P. "Red" Gribbin and William B. Baylor had acquired the rights to build dynamic brakes for rigs in 1946. The eddy-current braking system does not depend upon water pressure to work and is not at risk in the case of burst connections. Moreover, the dynamic brake can handle the cyclic overloads often encountered when floating vessels heave in ocean swells. In 1954, they formed the Baylor Company to build and install "Elmagco" Brakes. They were assisted by H.L. "Duke" Zinkgraf who modified and improved the design, adding a new control system. So effective was their product that it can be said that every offshore rig utilizing a subsea BOP system is equipped with the Baylor-Dynamic Elmagco Brake.
Recognizing the pioneering efforts of the following people and companies who contributed to the development of this technology:
William B. Baylor, H. L. "Duke" Zinkgraf
The Baylor Company
Underwater Wellheads
1999
The first underwater completions were a series of gas wells on the north shore of Lake Erie. Designed to avoid ice damage, trees were installed by suited divers in 20- to 30-ft of water. Shell's RUDAC System used a nested suspension system incorporating casing and tubing hangers, master valves and dual flowline connections for introduction of remote, through-tubing maintenance tools. The concept was first used in West Cameron 192 in 150-ft of water in 1960. Meanwhile on the west coast, Shell used a free-swimming remote-controlled robot, called MOBOT, to make up bolts and operate valves. Five wells at Gaviota were completed this way starting in 1962.
Recognizing the pioneering efforts of the following people and companies who contributed to the development of this technology:
John Haeber, Ron Geer, Bill Bates, Howard Shatto, Bill Petersen, Bruce Watkins.
WKM Valve (Cameron), Regan Forge & Engineering (ABB Vetco Gray), Shell Oil Co., Cameron Iron Works (Cameron)
Marine Risers Support Systems (Tensioners)
2000
The riser connecting a floating drilling vessel to the sea floor must be supported to keep it from buckling. Buoyant chambers provide sufficient uplift to keep the riser constantly tensioned and permit it to be free standing when not connected to the drilling vessel. However, there was a risk that should the riser become disconnected from the seabed it would bob to the surface damaging the rig. Thus, the idea was to keep the riser at neutral buoyancy using flotation and support it using tensioners, In the mid 1960's, The Rucker Company introduced their hydro-pneumatic tensioner systems using hydraulic pressure to stroke multiple compensation cylinders as the drilling vessel moves up and down. The hydraulic pressure is powered by air pressure stored in accumulators. The air either expands or is compressed as the cylinder rods stroke in and out. Cables run from the rods over sheaves mounted under the drill floor and are connected to the top of the riser keeping it positively tensioned. This same technology is used on the majority of floating drilling vessels today.
Recognizing the pioneering efforts of the following people and companies who contributed to the development of this technology:
Douwe "D" de Vries, John W. Prud'homme, Aaron "Dusty" Rhodes, George Savage,
Global Marine (GlobalSantaFe),
The Offshore Company (Transocean Inc.),
Petroleos Mexicanos (PEMEX),
The Rucker Company (Shaffer a Varco Co.), Shell
Marine Riser Systems
2001
A major technical problem facing the early designers of floating drilling equipment was to devise a method for providing a closed-circuit mud circulating system between the well at the sea floor and the drilling vessel at the surface.
In 1946, Union Oil Co. of California (Unocal) and Continental Oil Co. (Conoco) formed a joint venture to obtain cores offshore from floating vessels. In 1948, Unocal filed a patent on a technique using a marine riser to provide both a conduit for the drill pipe and a necessary return path for mud and cuttings.
By 1953, Unocal and Conoco had been joined by The Superior Oil Co. and Shell Oil Co. in an organization called the CUSS Group. CUSS installed a coring rig on a small wooden hulled ex-Navy patrol craft, the Submarex, and successfully drilled holes as deep as 2,700 feet in shallow waters off the coast of California. At that time however, return circulation was provided by rubber hoses connected to a circulating head which sealed around the drill pipe at the seabed.
In 1957, the CUSS Group, using the vessel CUSS I offshore California, and the Offshore Co., using the vessel D-1 offshore Trinidad, successfully implemented a true marine riser. Both designs incorporated a slip joint at the top to accommodate vessel heave.
Enhancements were provided in 1963 when the Offshore Co. added control lines and choke and kill lines to the basic riser configuration. Later improvements involved the means for latching individual riser sections together. The leader in developing these coupling improvements is generally acknowledged to be Regan Forge and Engineering Co.
Recognizing the pioneering efforts of the following individuals and companies who contributed to the development of this technology:
Robert F. Bauer, George Savage, Bruce Watkins
CUSS Group [Conoco, Unocal, The Superior Oil Co. (ExxonMobil) and Shell Oil Co.], The Offshore Co. (Transocean Inc.), and Regan Forge (ABB Vetco Gray).
High Holding Power Anchor Development
2002
Anchors for floating vessels have evolved from ancient times. The earliest anchors were stones that had holding power of less than their own weight. By the early 1900s the stockless anchor had been developed. That style anchor was, and still is, widely used on merchant and naval ships because it is easily stowed in the hawse pipe. The stockless anchor has a holding power of about twice its weight in air. In the late 1930s Richard S. Danforth and his nephew, Robert Danforth Ogg, developed the theory and designs for a light weight, drag embedment anchor. U.S. Patent 2,249,546 was granted to Richard S. Danforth on July 15, 1941. The Danforth anchor developed holding power of about ten times its weight in air and was widely used on landing craft during World War II.
The U.S. Navy built on Danforth's work and developed the STATO anchor with a holding power of about twenty times its weight. Mr. R.C. Towne, of the U.S. Naval Civil Engineering Laboratory at Port Hueneme, California, was instrumental in that effort and that organization published standardized test data on anchor holding powers that has been very useful to the offshore industry. In subsequent years numerous specialized, high holding power anchor designs have been developed for the offshore construction and drilling industries. These specialized anchors have holding powers of about twenty five times their weight and were a vital component in the large drilling and construction vessels for areas such as the Gulf of Mexico and the North Sea.
Some of the pioneers in these more recent developments are Peter Bruce, of Bruce Anchor Limited in the U.K.; Rob van den Haak, of Vryhof Ankers B.V. in the Netherlands; and Peter J. Klaren, of Anker Advies Bureau B.V. in the Netherlands.
Recognizing the pioneering efforts of the following individuals and companies who contributed to the development of this technology:
Richard Stevens Danforth, Robert Danforth Ogg, Richard C. Towne, Peter Bruce, Rob van den Haak, Peter J. Klaren
U.S. Naval Civil Engineering Laboratory, (Naval Facilities Engineering Service Center), Bruce Anchor Limited, Vryhof Ankers B.V., Anker Advies Bureau B.V. (Wortelboer Jr. B.V.)