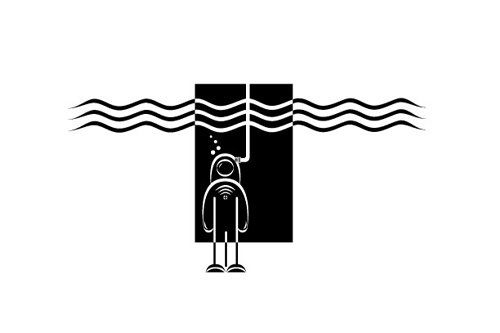
Subsea Technologies
Diving
1998
In 1905, the U.S. Navy began development of more modern equipment, diving tables, and diving practices using experience from worldwide operations. In order to go deeper and remain longer at depth, Commander George "Papa Topside" Bond started research for the Navy in 1957 leading to the development of "saturation diving." Bond perfected the equipment and diving tables through the "Genesis" program and the "seaLab" phases of activity. Dr. Robert Workman, a U.S. Navy Physiologist, was primarily responsible for the development of diving tables needed for saturation diving which uses a breathing mixture of helium and oxygen. In 1957, Edward Lee Taylor and Mark Banjavich, two ex-Navy divers, along with French diver Jean Valz, formed Taylor Diving & Salvage, later acquired by Brown & Root. They developed the techniques and equipment necessary (recompression chambers for surface decompression) to extend the use of mixed-gas diving to the deeper depths required by the offshore industry. Swiss physicist Hannes Keller, together with Shell Oil, experimented with diving to depths of 1,000 ft offshore California in the mid-1960s using helium-oxygen. His efforts led to further development of the diving tables used in mixed-gas diving. In the early 1970s and for 10 years thereafter, Shell started the development of Remote Operated Vehicles (ROVs) to conduct deep offshore inspection activities to supplement, and in some cases replace, the necessity to use divers. The first subsea completion was installed by Shell in the Gulf of Mexico in 1961, West Cameron Block 192, water depth 17 m (57 ft), as a test case for later deepwater application. Saturation diving was first used offshore in 1967 to install Shell's Marlin System at 320 ft in the West Delta field.
Recognizing the pioneering efforts of the following people and companies who contributed to the development of this technology:
Mark Banjavich, Robert "Bob" Barth, George F. Bond, Hannes Keller, Walter F. Mazzone, Edward L. Taylor, Jean G. Valz, Robert D. Workman
Shell, Taylor Diving (Halliburton), U.S. Navy
Remotely Operated Vehicles (ROVs)
2009
In the early 1960’s Shell Oil started development of the first ROV, named “Mobot” that was tethered to the surface and equipped with a TV eye, sonar, gyrocompass, thrusters and hydraulic arms. It operated somewhat successfully; however, through the remaining 1960’s into the late 1970’s the industry used manned manipulator bells, manned submersibles and “eyeball” only ROVs. During this period, service companies worked on integrating sophisticated electronics and hydraulics into the ROV concept but with oilfield robustness.
In 1976 and 1977 a number of companies made significant advances in the development of ROV technology with a number of models (Deep Drone, Scorpio, SCARAB, Hysub and TROV) being used in the oilfield, government programs and in research though they had many technical and operating problems. The development of the Hysub ROV by ISE and Perry was the technical foundation of today’s ROVs. The development of launch system with subsea top hat tether management systems and “cages” also allowed deployment in rougher environmental conditions with less risk of damage or loss. The industry also developed “tooling” that interfaced with sophisticated subsea equipment that had touch and load arm feedback. Consolidation of companies (Oceaneering and Solas Ocean Systems, etc.) in the 1980s provided the critical mass to move the industry forward. Following years saw ROVs become more capable, versatile, reliable and powerful where almost every floating drilling rig and construction project offshore today uses them on a daily basis.
Recognizing the pioneering efforts of the following individuals and organizations that contributed to this technology:
Bruce Watkins, Howard Shatto, Richard “Dick’ Frisbie, Drew Michel, Walter Gray,
Herb Newberry, Hydro Products, Sub Sea International (now Subsea 7), Ametek (Straza Division), British Petroleum (now BP), International Submarine Engineering (ISE) Ltd., Oceaneering International Inc., Ocean System Engineering Ltd, Perry Oceanographic (now Perry Slingsby Systems, A member of the Triton Group), Phillips Petroleum (now ConocoPhillips), Saab Underwater Systems, Shell Oil Co. and Taylor Diving.
Subsea Wet-Mateable Electrical Connectors
2016
Today’s applications for wet-mateable connections include high-power lines, low-power data links, hydraulic fluid lines, and fiber-optic cables. Each has formidable challenges. Complex umbilicals may combine all of these applications in a single multi connection plug-in. The design must exclude even the smallest drop of highly-conductive sea water. In the early 1990s, reliable wet-mateable connectors became available, but the challenge was not over. The industry required that connections could be made in water depths beyond that accessible by divers. So plugs and sockets had to be modularized into connections that could be handled by Remotely Operated Vehicles (ROV). Today, plug-n-play (PNP) components can be routinely connected on the sea bed. Shell’s Popeye installation was performed in 2,000-ft of water without incident. Applications of modern wet-mateables include:
- Downhole electrical sensors and instrumentation
- PNP subsea modules
- Flexible architecture that allows additional equipment installations at a later date
- Simple interconnections between modules in-situ
- High-power supply for subsea processing.
Recognizing the pioneering efforts of the following individual and organizations that contributed to this technology:
James L. Cairns, Ph. D SEACON Group, Teledyne ODI, and Tronic (now Siemens)
Electrical and Hydraulic and Flying Leads
2017
Modern subsea oil and gas production requires hydraulic power and electrical signals to operate and control its various components. Before reliable wet-mateable conductive
connectors became available, the industry had only limited means to establish electrical connections between subsea components. The origin of the flying lead can probably be
traced back to Shell’s deepwater drilling program off the USA east Coast 1983. They made provisions for the ROV to deploy and mate flexible hydraulic tubing on the lower marine
riser package. Following that experience, and with the availability of reliable wet-mateable connectors and the maturation of the ROV as a capable subsea robot, the technology was
advanced to deploy and connect electrical and multicore hydraulic “flying leads” between subsea components as far away as 200 feet.
- This technology allows: subsea architecture with multiple smaller modules placed on the seabed, installed and retrieved with modest and widely available surface equipment;
- flexible subsea architecture allowing the addition of equipment at a later date when needed (e.g. subsea pump modules when reservoir pressure is in decline); relatively simple
- and inexpensive interconnections between modules made by ROV using flexible umbilicals (flying leads).
Recognizing the pioneering efforts of the following individuals and organizations that contributed to this technology:
Dick Frisbie, Howard Shatto, Mike Williams and Tom Williams
FMC (now TechnipFMC), Oceaneering and Shell
Subsea Pumping and Compression (Boosting)
2018
Conventional pressure boosting has been important to the oil and gas industry for many years with pumping technology routinely used to move oil and gas long distances from points of production to storage, refining and shipment.
Since the early 1980’s, much effort has been expended to adapt these long-used and proven conventional boosting technologies to more challenging subsea production applications to facilitate the movement of subsea production to receiving or processing facilities.
Taken collectively, subsea boosting can help make marginal fields viable and can extend the useful life of existing fields, while also permitting tiebacks from long distances and great depths.
Many challenges had to be overcome to adapt boosting equipment to subsea use including: ‘marinizing’ equipment, delivering power and controls over long distances, and accommodating full well-stream flows. Research and development were fostered by government policy and joint industry programs, and private companies contributed significantly to the technology advancement.
Companies honored are a subset of the many contributors to the research and development of subsea pressure boosting systems: ExxonMobil, Framo (now Schlumberger), Nuovo Pignone (now Baker Hughes, a GE company), Petrobras and Statoil (now Equinor).