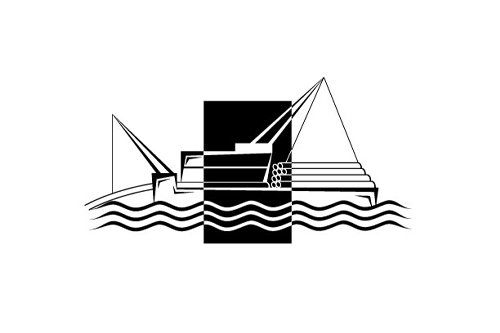
Drilling Technology
Mobile Drilling Units: Jackup Rigs
1998
Offshore Rig 51 was the first self-elevating drilling unit. It went into service in 1954. The Offshore Company was developed as a joint venture with Southern Production (now SONAT), J. Ray McDermott and DeLong. Based on the DeLong jacking system the rig had 10 legs, each 6 ft in diameter and 160 ft long, with large spud cans to limit penetration into the seafloor. By means of a jacking and holding mechanism, the barge pulled itself out of the water, safely above the waves.
Mr. Gus was a Bethlehem design, self elevating unit and was built in 1954 for C. G. Glasscock Drilling Co. intended for 100 ft water depth operations. The forerunner of today's fleet of jackups was the Scorpion. Designed by R. G. Le Tourneau and built by the Le Tourneau Company in 1956, it was a triangular platform with 3 trussed legs. Each leg had a full length gear rack to engage the pinions of the elevating mechanism. Pinions were driven by powerful electric motors equipped with electromagnetic brakes. The Zapata Offshore Co., who had the foresight to purchase this innovative jackup design, was headed by future US President George Bush.
Recognizing the pioneering efforts of the following people and companies who contributed to the development of this technology:
George H. W. Bush, Colonel Leon B. DeLong, Charles G. "Mr. Gus" Glassock, Robert G. Le Tourneau, Ralph Thomas "J. Ray" McDermott, F. "Tim" Pease, James E. Steele, James C. "Jimmy" Storm Bethlehem Steel, Le Tourneau Inc., J. Ray McDermott Co., The Offshore Co. (Transocean Inc.), Zapata Offshore Co. (Diamond Offshore)
Mobile Drilling Units: Submersible Rigs
1998
In 1928 Louis Giliasso filed a patent for a submersible drilling barge based on his experiences in Lake Maracaibo, Venezuela. The first submersible went to work for The Texas Company on November 17, 1933 at State-Pelto No. 10, Louisiana. It was equipped to drill to 6,000 ft and operate in 15 ft of water. John Hayward saw the opportunity to combine a barge and a piled platform, so that the rig's working decks were above the water and only the columns connecting to the submerged barge were exposed to wave forces. He developed a method for ballasting the barge to the seafloor without it becoming unstable and overturning. The Breton Rig 20 was conceived by Hayward and built for Barnsdall Oil & Refining Co. getting into operation in 1949. It drilled 19 wells before being sold to Kerr-McGee in 1950. An improved version of the submersible was developed by Alden J. "Doc" Laborde, a young Naval engineer, who founded Ocean Drilling and Exploration Co. (ODECO) in 1953. The rig was built in Alexander Shipyard in New Orleans, and was named Mr. Charlie after Charles Murphy, President of Murphy Oil. Its first well was drilled for Shell in the East Bay Field, near the mouth of the Mississippi in 1954. Water would be pumped into the barge to sink it. When resting on the bottom, it formed a stable platform from which to drill. When the drilling was finished, the submersible could be refloated and towed to the next location. Mr. Charlie is now a museum in Morgan City, Louisiana.
Recognizing the pioneering efforts of the following people and companies who contributed to the development of this technology:
Emile J. Brinkmann, Jr., Louis Giliasso, Jerome L. Goldman, John Hayward, Alden J. "Doc" Laborde, Charles Murphy, Jr., Paul Wolff Barnsdall Oil & Refining Co. (Oryx Energy), Kerr-McGee, Murphy Oil, ODECO (Diamond Offshore), Shell, The Texas Company (ChevronTexaco)
Mobile Drilling Units: Tender Rigs
1998
Initial offshore drilling was carried out using small, piled platforms. The equipment, supplies, and personnel were housed on converted LSTs (Landing Ship Tanks) and Y-F (Yard-Fighter) barges, which after 1947, were surplus from World War II. These vessels were known as "tenders" (named after the coal-carrying tenders coupled to steam train engines). R.S. Kerr pioneered the use of tender rigs and is chronicled as the first to strike oil out of sight of land in 1947 in Ship Shoal Block 32. Phillips Petroleum Co. (50%) and Stanolind Oil and Gas Co. (37.5%) were partners in the well. Kerr-McGee acted as driller and operator. The tender was Frank Phillips. The prototype of the Kerr-McGee tender approach was introduced in Lake Maracaibo, Venezuela, in 1934 and prior to that similar setups had been used in the marshy areas of the Gulf coast. Oil companies bought LSTs and refitted them for offshore purposes after this first discovery. For the next several years, 90% of the offshore wells were drilled from tender-platform combinations.
The narrow gangplank connecting the heaving tender with the stationary platform was called the "widow-maker" with good reason.
Recognizing the pioneering efforts of the following people and companies who contributed to the development of this technology:
Robert S. Kerr, Sr., Frank Phillips Kerr-McGee, Phillips Petroleum, Stanolind (BP)
Subsea BOP Control Systems
2001
The earliest floating drilling operations were carried out with direct control lines from the vessel to each function on the BOP stack. Many innovations were required to make these systems suitable for deeper water and separately retrievable. The pioneering innovators of subsea BOP control systems were individuals with Payne Manufacturing Co., Koomey Division of Stewart & Stevenson Distributing Co. and Hydril Co. The following table summarizes important developments of these systems.
- 1953, Submarex, Koomey, Directed connected control lines, Air operated hydraulic plunger pumps.
- 1955, CUSS I, Hydril, Electric Hydraulic Plunger Pumps, 80 gallon, 1500 psi accumulators.
- 1961, Bluewater 1, Koomey, 3000 psi accumulators with two pressure-reducing/regulating valves.
- 1963, Ocean Driller, Payne, Bundled controlled hoses and retrievable control pods.
- 1967, STAFLO, Koomey, SPM valves and choke & kill lines incorporated in control pods
- 1968, Bluewater II, Koomey Martin-Marietta, Nuclear powered subsea hydraulic pumps and acoustic controls, tested but non-commercial.
- 1968, Glomar V, Koomey, Compact design packer seal pods
- 1968, Sedco 445, Koomey, First electro-hydraulic controls and 6000-psi accumulators
- 1970, Discoverer, Koomey, First Multiplex (MUX) control system
Recognizing the pioneering efforts of the following people and companies who contributed to the development of this technology:
Harry Burgess, Paul Koomey, Joe LeMoine, George Lewis, and Hershel Payne
Hydril Co., Koomey Division of Stewart & Stevenson Distributing Co. (Shaffer Division of Varco International) and Payne Manufacturing (Cameron).
Development of Offshore Drilling Equipment
2003
Control of well pressures during drilling, completion and production is a fundamental requirement for the safe production of oil and gas. Perhaps more innovative technology has been developed to solve this problem than any other. Key developments include the ram-type blowout preventer (BOP) and the annular BOP. Other systems were built to control subsea wells and allow safe access for periodic maintenance.
Marvin R. Jones invented the Cameron Type U subsea ram preventer. Born in Bristow, Oklahoma in 1914, Jones began his career with Hughes Tool Co. In 1939, he joined Cameron Iron Works. Following his WW II service, he worked in oilfield engineering until he rejoined Cameron in 1955. During the next 24 years, he progressed from Sr. Research Engineer to manager of Engineering Services. Jones was granted about 70 patents.
Granville Sloan Knox invented the annular blowout preventer that was modified for use on subsea BOP stacks. He was granted more than 30 patents. Born in Earlham, Iowa in 1907, Knox joined Hydril in 1936 as a draftsman. His value was quickly recognized and he was promoted to Engineer that same year. He was promoted to Assistant Chief Engineer in 1943 and to Vice President in 1952. He retired in 1965 and died in 1998.
Hubert L. “Hugh” Elkins has spent 48 years in the offshore oil industry and has been granted numerous patents. Working for S&R Tool and Supply Co., he designed and built the subsea BOP guide frame structure that is the industry standard. In 1973, he joined Hydril, serving in a number of executive engineering posts before retiring in 1993. Elkins is presently Director of Business Development for Varco’s Shaffer Division, and serves on the Technology and Engineering Development Committee for the Ocean Drilling Program.
Edmund A. “Ed” Fisher pioneered the subsea Christmas tree diverter systems used with ThruFlowLine tools. He also developed the guidelineless drilling systems used by the Ben Ocean Lancer and the Freestanding Production Riser System for Placid Oil Co. Starting in 1961, Fisher spent almost 40 years with Cameron, retiring in 1999 as Executive Vice President. In 1995 Fisher received the prestigious Oil Drop Award of the ASME Petroleum Division.
Recognizing the pioneering efforts of the following individuals who contributed to the development of offshore drilling equipment:
Hubert L. “Hugh” Elkins, Edmund A. “Ed” Fisher, Marvin R. Jones, Granville S. Knox
Drillstring Motion Compensators
2004
With the advent of drilling offshore wells from floating drilling vessels in the late 1950’s came the inherent problem of how to keep the drillbit on bottom and drilling while the drilling vessel heaved up and down. The answer at the time was to use a tool developed by the oilwell fishing tool industry known as a “Bumper Sub”. This tool was simply a slip joint that was placed above the drill collars that would allow the drillpipe to move up and down while the drill collars and bit remained on bottom. Most Bumper Subs were limited to a stroke of only six to eight feet. The Driller had to continually estimate the heave of the drilling vessel as well as the drilling penetration rate trying to keep the Bumper Sub from bottoming out at either end of its stroke. If the sub bottomed out the bit would bounce off bottom with the entire weight of the Drillstring usually damaging and shortening the life of the bit. A good Driller became an artist at keeping the bit on bottom most of the time.
However, there was one problem that the Driller could not overcome. That is the fact that the high-pressure mud seals in the Bumper Sub only had an average life span of around thirty to forty hours. This meant that the Drillstring had to be tripped to refurbish the Bumper Sub before the seals wore out causing a leak that would wash out the Bumper Sub and allow the Drillstring to part. Since the life of most drillbits exceeded the life of the Bumper Sub more than the usual amount of costly Drillstring trips were required. Over the decade of the 1960’s floating drilling had to contend with the Bumper Sub though new type seal technology did make for up to three times better life. There needed to be a better answer and much pressure was placed on the drilling equipment manufacturers to find another method of Drillstring motion compensation to replace the Bumper Sub.
In about 1970 three companies began to put major effort into development of a tool that could be placed on the rig at the surface to compensate for and separate the Rig’s motion from the Drillstring. These companies were Ventura Tool Company (VETCO), Rucker Company, and Western Gear Company. Each chose a variation of the successful hydro pneumatic Marine Riser Tensioner technology developed in the early 1960’s. Vetco was the first to install a successful prototype system in 1971 on the Wodeco IV in the Santa Barbara channel for Humble Oil Company (now ExxonMobil).
Rucker and Western Gear followed this closely in 1972 with deliveries to customers of their first production Compensators. All three systems worked well and were a successful solution to the Bumper Sub problems.
Though the three systems were somewhat different in design each is mounted in the derrick between the Traveling Block and Hook and all use compressed air as a spring force to hold positive tension on the Drillstring. Each allows for better control of the bit weight resulting in much better bit life and drilling penetration rates. Since they are mounted as part of the traveling system in the derrick not all of the older rigs prior to the 1970’s could be readily retrofitted with the new Motion Compensators. By the mid 1970’s all new floating rigs built were either equipped with or the derricks were prepared for later installation of Drillstring Motion Compensators
The three original Compensator designs are still in existence with many improvements and much higher capacity systems though the ownership of the three original companies has changed. The Rucker Company Compensator product line, which has been owned by Shaffer since 1972 is now owned by Varco International. Control Flow Company who service and market both products now owns the Vetco and Western Gear Compensator product lines.
Vetco, Rucker Company and Western Gear will be recognized as the originators of the technology and Varco and Control Flow will be recognized as the current technology owners.
Recognizing the following individuals and companies who contributed to the development of this technology:
Arthur Hor Ting Chin, Bruce Duncan, James Hanes, Edward Larralde, Glen Robinson, Richard Sprague, Rucker/Shaffer (now Varco International), Ventura Tool Co. and Western Gear (now Control Flow Inc.).
Top Drive Drilling Systems
2006
Top Drive Drilling Systems are one of the greatest contributions to the offshore drilling industry. Until 1982 the drillstring was handled and rotated by a Kelly Joint and a Rotary Table. Drilling and making connections on offshore rigs had been virtually unchanged for years. Then development of the Top Drive, which rotates the drillpipe directly and is guided down rails in the derrick, replaced the need for a Kelly Joint to rotate the drillstring. It performs normal hoisting requirements such as tripping and running casing. It also added the ability for drilling with triples, circulating and rotating during tripping, and back-reaming and/or freeing stuck pipe. The first use of this unique technology was in 1982 on a Sedco Jack-Up rig drilling for ADNOC in the Arabian Gulf. Working with Duke Zinkgraf of Sedco, George Boyadjieff of Varco designed a Pipe Handler as part of the Top Drive. This unique feature allowed back-reaming while circulating drilling fluid and making/breaking connections near the top of the derrick.
Recognizing the pioneering efforts of the following individuals and companies who contributed to the development of this technology:
George Boyadjieff, Varco International (now National Oilwell Varco); Duke Zinkgraf, Sedco (now Transocean).
Spiral Drill Collar
2007
The spiral drill collar, invented and developed by Fred K. Fox in 1961, prevents or mitigates the problem of differential pressure wall sticking of drill collars leading to stuck drill strings, a prevalent problem encountered in drilling deep, high pressure and deviated wells.
Grooves spiraled around the outer surface of the collar interrupt contact of the collar with the wall of the bore hole. In subsequent years, the spiral concept has been expanded to casing, liners, wash pipe, and heavy weight drillpipe. Spiral collars are used worldwide to this day in virtually all moderate to deep offshore and onshore wells and in all deviated and horizontal holes.
Recognizing the pioneering efforts of the following individuals and companies who contributed to the development of this technology:
Fred K. Fox
Heavy Weight Drill Pipe
2008
The need for a bottom hole assembly to prevent wall sticking that would be flexible enough to be used in directionally drilled holes was noted by a major oil company engineer at an API meeting in New Orleans, circa 1962. The company had tried using two pieces of concentric pipe with tar between the members.
Called “flex weight”, this configuration could not withstand the environment in directional offshore wells. Glenn Chance, the local Drilco district manager, attended that API meeting. It occurred to him that welding tool joints on the ends of used drill collars might address the problem and, if successful, would significantly reduce drilling costs. For a second opinion, he consulted with Clifford Yancey of Rowan Drilling Co. in New Orleans, who agreed with the theory and two pieces were made. These proved to be too stiff. Drilco in Houston then turned the outside diameter on 30 used drill collars, leaving one wear pad 3-ft. long and welded 5-in. tool joints on each end. Unfortunately, the concept was not acceptable to operators until Albert Crownover, Tenneco’s drilling manager, agreed to run the pipe, which performed as expected. Drilco then modified 120 more collars, but the concept remained a tough sell to operators until J. B. N. Morris of Canal Rental, convinced Shell Oil Co. to test the idea and Bob Turnbull of Turnbull Rentals did the same. Ultimately, the concept became a standard for directional wells both on land and offshore, and was marketed under the name Hevi-Wate Drill Pipe. Since used drill collars soon became in short supply, Drilco engineer Sam Crews enlisted Timco Roller Bearings to produce a one piece, 27-ft. long, 5 ½-in.OD x 3-in. ID joint, with the specifications of Grade E drill pipe. Drilco built a machine which would fast turn the OD of the joints, leaving a 3-ft. wear pad in the middle. In 1977, Glenn Chance organized Chance Collar Co. By then, spiral drill collars had become a standard in directional drilling so Chance incorporated the spiral concept in his heavy weight product. Sales grew to some 3,500 pieces per month with a total value of a billion dollars annually and enabled worldwide development of offshore drilling.
Recognizing the pioneering efforts of the following individuals and companies that developed this technology:
Glenn G. Chance, Sam T. Crews and Drilco (now Smith International)
Measurement While Drilling (MWD)
2011
When drilling oil and gas wells, it is necessary to determine geological properties of the formation and direction of the wellbore. Historically this was accomplished by running a wire line to the bottom of the uncased wellbore. Devices attached to the wire line transmitted desired data back to the surface. This required suspension of drilling operations and retrieval of drill pipe from the wellbore. Besides lost drilling time, other problems could occur, such as borehole sloughing or stuck drill pipe. In 1945, J. J. Arps invented a positive mud-pulse system that could measure formation data and transmit it to surface while continuing to rotate drill pipe and circulate drilling mud. In 1964, J. K. Godbey filed a patent for improving mud-pulse telemetry with his “Mud Siren System”, field tested by Mobil Oil in 1971, and then developed commercially by Schlumberger/Anadrill in 1980.
In 1969, Jean-Claude Raynal, with Elf Aquitaine, filed a patent for a drilling mud-pulse generator to measure and signal real time mechanical properties of the formation to the drill floor while drilling; and in 1974, Ralph Spinnler, with Teleco, filed a patent for a pilot operated mud-pulse valve that used a small input signal from drilling mud pressure differentials, which greatly improved reliability of mud-pulse technology. Subsequent advances in MWD techniques now allow controlling well direction and real-time formation evaluation with resulting safety aspects and drilling optimization. MWD is currently used in virtually all offshore drilling operations.
Recognizing the pioneering efforts of the following individuals and organizations that contributed to this technology:
J. J. Arps, J. K. Godbey, Jean-Claude Raynal, and Ralph F. Spinnler. Mobil Oil Corp. (Now ExxonMobil), Schlumberger, Teleco (now Baker Hughes) and Elf Aquitaine (Now Total).
Drill Floor Mechanization and Automation
2012
In the late 1940s, the Humble Oil & Refining Company, with a group of suppliers, pioneered development of the industry’s first “mechanized” rotary drilling rig to increase drilling efficiency and safety by improving the way drilling tubulars were made, torqued and racked. It featured power-operated tongs with spinner, stabber and vertical racking equipment.
In the 1950s and 1960s, the mobile offshore drilling units (MODUs), particularly floaters, faced unique problems due to their motion in the severe marine environment. This focused renewed attention on mechanization and automation.
A major step forward was the introduction of horizontal-to-vertical (HTV) mechanical handling of drilling tubulars on Global Marine drill ships in the 1960s. Simultaneously, the Offshore Company and Byron Jackson developed the 3-arm tubular racker. The system was highly successful and racked pipe faster and safer than “hands-on” drill crew methodology. One and two arm versions were adapted to all MODUs. Varco followed in the 1970s with its “Iron Roughneck” that could accurately torque drill pipe, drill collars and other types of tubulars. Other innovations appeared, such as air operated mouse hole slips, power rotary slips, and air or hydraulic powered casing elevators and slips, capped by the power swivel for smaller tubulars, followed by Varco’s “Top Drive” for large drill pipe and tools. Combined, these features allowed a mechanized and automated operation that included “safe zones” monitored electronically to prevent equipment from harming drill crews. Innovative software prevented clashes by tracking the locations of the equipment. Subsequent advances include a “raised back-up” system to safely make/break connections high above the drill floor and the HTV marine riser handling system. In the late 1980s, the technique of makeup/breakout and standing back tubulars “offline” from the “online” rotary was developed.
Recognizing the pioneering efforts of the following individuals and organizations that contributed to this technology:
Curtis Crooke, John F. Gadbois, Douglas Ragland and Roger Smith.
Global Marine (now Transocean), Humble Oil & Refining Company (now ExxonMobil), the Offshore Company (now Transocean) and the Byron Jackson Company (now National Oilwell Varco).
Marine Drilling Riser Phase I Analysis
2013
The primary purpose of a drilling marine riser system is to allow circulation of fluids into and out of the wellbore, help maintain well control, and guide items into and out of the wellbore. The roots of riser analysis start with the Mohole project in 1950. The first floating drilling rigs to utilize a metal marine riser were the CUSS 1 (Continental, Union, Shell, and Superior Oil) and D-1 (Offshore Co.) in 1957. Initially for very shallow water, simple column analysis was considered adequate but as water depths increased the industry realized it was necessary to understand the physics, materials of the structure and operating parameters to recommend adequate top tension and vessel position limits.
The technology advanced slowly until floating drilling became a priority for several oil companies. In 1965, the CUSS 1, drilling for Humble Oil & Refining Co., set a world water depth record of 632 feet in the Santa Barbara Channel and was a precursor for the deepwater Santa Barbara Channel OCS lease sale in 1968. Key operators were Chevron, Shell Oil, and Humble Oil, each building and modifying floating rigs while developing proprietary technology. It was apparent to these companies and emerging riser manufacturers that more comprehensive riser analysis methods were needed for the static and dynamic issues in deepwater riser analysis, design and operation.
Between 1965 and 1973, several professional papers had been published, revealing much of the early analysis technology. The critical effect of mud density on required riser tension was discovered and named the effective tension principle. By 1973, riser analyses had incorporated dynamic behavior from wave-induced motions of the riser and the vessel.
This first phase in the ability to analyze, predict behavior and operate drilling risers was a key factor in the successful evolution of floating drilling to 1,500 feet of water, laying the foundation for future advances to greater water depths.
Recognizing the pioneering efforts of the following individuals and organizations that contributed to this technology:
Gerald L. Barksdale, Ben G. Burke, Mark A. Childers, William Fischer, Clinton Gosse, John Lacy, Milton Ludwig and Danny R. Tidwell,
Cameron Iron Works, Esso (now ExxonMobil), Shell and Standard Oil (now Chevron).
Marine Riser Analysis Phase 2 (1973 to 1985)
2014
The marine riser is used in drilling as a pathway between a floating drilling rig and the subsea well during drilling. For production, the riser provides a vertical pipeline that carries oil and gas from the sea floor to the floating production platform. Both are essential for deepwater oil and gas development.
The advances in the 1970’s were consideration of riser dynamics in loads, environment, and the response motions of the riser. In the 1980’s, use of riser equations was facilitated by the rapid evolution of computing power. The more powerful computers enabled more thorough and accurate analysis techniques.
A pioneering program version was called ‘DERP’ (for ‘Darned’ Efficient Riser Program), developed by Stress Engineering Services (SES) working for Cameron Iron Works. Lawrence Krolikowski and Tom Gay (Exxon Production Research Co.) joined with the SES engineers to develop computational advances involving linearization for the frequency domain. In the early 1980s, DERP was extended to the industry, and became available for customer PCs. The sensitivity of the riser analysis results to operating input parameters challenged analysts and operations people to use design bases that were both practical and provided adequate safety margins. In the early years, each offshore operator and contractor developed their own design parameters. Mark Childers cataloged the resulting wide variation in recommended tensions and in 1980 published the first suggested uniform parameters.
An API Task Group chaired by Paul Stanton worked through the many technical and risk issues facing industry-wide standard parameters and published RP 2Q “Design and Operation of Marine Drilling Riser Systems” in 1984. With Phase 2 technology, drilling marine risers moved to 7,500 feet of water depth by 1987 and in to 10,000 feet in 2004. Comprehensive analysis, appropriate safety margins, and sound operation of marine risers have been essential to working in deepwater and hostile offshore environments.
Recognizing the pioneering efforts of the following individuals and organizations that contributed to this technology:
Mark A. Childers, Early Denison, Joe Fowler, Allen Fox, Terry N. Gardner, Tom Gay, Lawrence P. Krolikowski, Joe Roche, Charles P. Sparks, Paul Stanton, Riddle Steddum, and Ron Young Cameron Iron Works, Exxon Production Research Company, Hydril (now GE Oil & Gas), Institut Français du Pétrole (now IFP Energies nouvelles (IFPEN)), Mechanics Research Institute, Shell Oil Company, Sonat Offshore Drilling (now Transocean), and Stress Engineering Services
Horizontal Drilling
2014
Wells that are vertical, perpendicular to the petroleum formation, are often uneconomic, but drilling the lower part of the well horizontally, paralleling the reservoir, greatly increases their production rate. While this was long recognized, effective technology was elusive until 1982 when the Elf Aquitaine offshore Rospo Mare field in the Italian Adriatic was developed with horizontal drilling.
Independently 1979 to 1982, an effort was undertaken by ARCO with 12 horizontal wells in New Mexico. This work led to the development of the medium radius technique, a critical improvement over the previous short radius and long radius methods. In 1985, a medium radius horizontal well was successfully drilled by ARCO at the Prudhoe Bay oil field to manage a fluid coning issue.
From 1985 to 1992, the technology was rapidly expanded and its use broadened by a joint industry horizontal drilling research project, DEA-44, with about 50 participating companies. The project also developed the medium radius drilling motor.
Subsequent to the Rospo Mare field, many worldwide offshore developments have employed horizontal drilling, including Selegi (Malaysia), Joton and Ringhorn (Norway), Dan (Denmark), Buffalo and Gimboa (Angola), Widuri (Indonesia), Champion (Brunei), Al Shaheen (Qatar). Onshore, horizontal drilling has been used for naturally fractured formations such as the Texas Austin Chalk and later in numerous shale oil and gas developments, further enhanced by hydraulic fracturing.
Recognizing the pioneering efforts of the following individuals and organizations that contributed to this technology:
Jacques Bosio, André Jourdan, Dr. William Maurer, and Frank Schuh
Atlantic Richfield Company (now BP), Elf Aquitaine (now TOTAL), and Maurer Engineering.
Marine Riser Buoyancy
2015
Floating rigs used marine riser to guide items in and out of the wellbore on the sea floor. Air buoyancy tanks attached to the riser distributed the load. As operating depths increased, problems with air-can risers increased. In the late 1960’s pneumatic/hydraulic tensioners were invented that allowed larger tensions to be placed on the riser. This also isolated it from vessel motion. In the 70s, syntactic foam buoyancy was introduced. Humble Oil & Refining Co used syntactic foam buoys strapped on a 16 inch marine riser. In deeper water, foam buoyancy issues including water absorption, hydrostatic compression, impact resistance and attachment schemes were solved. Today syntactic foam is the backbone of deep-water riser technology, satisfying structural integrity for drilling and production risers.
Recognizing the pioneering efforts of the following individuals and organizations that contributed to this technology:
Hugh Bezner, Robert E. Bradbury Jr., Dave Cook, Dr. William R. (Bill) Cuming, George M. Savage, Bruce Watkins, and Lou W. Watkins
Emerson & Cuming (now Trelleborg Offshore), Humble Oil & Refining Company (now ExxonMobil), Offshore Company (now Transocean), and Regan Forge & Engineering Company (now GE Oil & Gas)
High Strength Pressure Flexible Joints
2016
In the early days of floating drilling it became apparent that a pivot point at the lower end of the marine riser next to the BOP stack was needed to reduce stress and fatigue in the marine riser. As water depths increased a new devise was needed. Lockheed Propulsion invented a pivot devise consisting of concentric spherical rings of steel separated and adhered to by elastomeric material that could with stand very large tensions and pressures. In 1976 the first subsea drilling “Flex Joint”TM was designed and manufactured by Oil States and used on a SEDCO rig. Following its successes in drilling, the technology was used in 1984 for the TLP tendons on the North Sea Conoco Hutton platform. In 1994 Shell used the device with steel catenary risers (SCR) on floating production systems. Since that time there has been over 700 versions of the Flex JointTM used in the offshore oil and gas industry.
Recognizing the pioneering efforts of the following individuals and organizations that contributed to this technology:
Mark A. Childers, Mike Hogan, Frans Kopp, Craig Lang, Carl Langner, Charles Moses, Charles Reinhardt, Earl Shanks and Jim Slade Conoco (now ConocoPhillips), Kingsnorth Marine Drilling, Lockheed Propulsion, ODECO (now Diamond Offshore Drilling Inc.), Oil States (now Oil States International, Inc.), SEDCO (now Transocean), and Shell
Polyester Deepwater Mooring Systems
2016
The use of polyester cables for deepwater mooring started in the 1980s by Marlow Ropes, a UK Company. Petrobras began installing polyester mooring systems immediately, leading to the P-19 and P-26 installations. Another program, set out to qualify advanced polyesters with standard polyester as a base case. The superior performance of standard polyester proved it to be the best solution at lowest cost. Leading the way were BP and Shell. BP installed the system on its Mad Dog platform and Kerr McGee equipped the first cell-spar, Red Hawk.
Recognizing the pioneering efforts of the following individuals and organizations that contributed to this technology:
Ray Ayers Ph. D., Steven Banfield, Luis Claudio Sousa Costa, Cesar Del Vecchio, Paul Devlin, Felix Dyhrkopp, John Flory, Jenifer Tule Ham, John W. S. Hearle Ph. D., Mike Parsey, David Petruska, Hongbo Shu, Richard Snell, Richard W. P. Stonor Ph. D.,Sim Whitehill, and Mitch Winkler, BP, BSEE, Chevron, DeepStar, Kerr McGee (now Anadarko), Marlow, Noble Denton (now DNV GL), Petrobras, RPSEA, Shell, Stress Engineering, Tension Technology Inc., and Whitehill Manufacturing Company